90 percent recycling rate, up to 92 percent lower CO2 emissions than the industry average and continual innovation: The Finnish company Outokumpu is the most sustainable stainless steel producer in the world. Its plant in Dillenburg, Hessen, is an important global interface – and home to the company’s 19,000 honeybees.
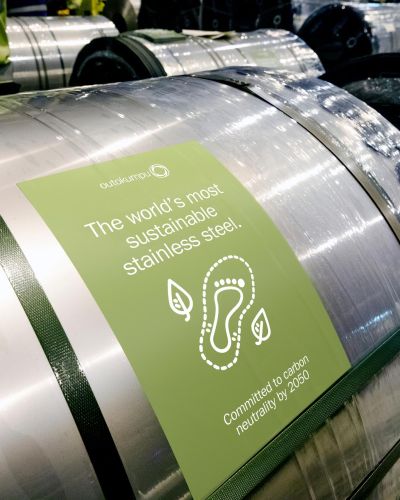
Sustainable stainless steel and fine wildflower honey from Central Hessen
“Sustainability and climate protection are also about mindset,” says Thorsten Piniek, Vice President of Outokumpu Nirosta GmbH and Head of Operations at the company’s site in Dillenburg in Central Hessen. And so, the highly specialized cold rolling plant of the world’s most sustainable manufacturer of stainless steel produces not only extraordinary materials – which have been used in the facades of buildings such as the One World Trade Center in New York and the Burj Khalifa in Dubai – but also honey, which 19,000 busy bees collect on the wildflower meadows of the plant grounds.
“This is a project for our trainees, who look after our five beehives and bottle the honey together with people with learning disabilities and the local Lebenshilfe charity. Of course, this initiative is only a very small step, but it is a meaningful one for our young employees: As a result, they experience the issue of sustainability in a very tangible way and develop a positive mindset. And they can later apply this mindset in many places within the company,” explains Piniek.
Employee expertise as a major locational plus
At the Finnish company’s plant in Central Hessen, there has long been a tradition of focusing on employees: Flat products made from stainless steel have been manufactured in Dillenburg for generations. The huge rolls of millimeter-thin material are used around the world by leading manufacturers of whiteware and cars, as well as for sophisticated facades and other architectural features. This makes the expertise of the employees a key locational advantage for Central Hessen, which Outokumpu supports with its own projects.
The region is ideal for us because this knowledge is irreplaceable for our business. And we find the transport connections excellent here: By motorway, and also by train, because around 90 percent of our primary material is delivered by rail. After all, it’s more sustainable than transport by truck.
Protecting the climate and the environment is a matter of course for Outokumpu – and a business advantage. “Our customers specifically ask about the carbon footprint of our products. And we are world leaders in this respect: We produce around 1.7 tons of carbon dioxide per ton of stainless steel across the entire value chain. In comparison, companies from Asia produce around 7.8 tons of CO2 for the same amount of stainless steel, on average,” calculates Thorsten Piniek. “And we’re always working on improvements: With our new Circle Green product line, we are actually 92 percent below the industry average in terms of CO2 emissions and another 64 percent below our own regular production.”
The key to this ‘green stainless steel’ lies in reducing emissions in the upstream raw material chain, as these account for the largest part of the overall carbon footprint. Outokumpu makes use of its own ferrochrome mine and smelter in Finnish Lapland, as Vice President HR Henrik Lehnhardt explains: “Thanks to this positive position, which is unique in Europe, we have complete control over all processes and can adjust them at any point. Through numerous production and quality optimizations as well as the use of biogas, biodiesel, biocoke and low-carbon electricity, we can enormously increase sustainability throughout our entire production. To date, no other manufacturer has been able to produce stainless steel with such low emission values,when considering the total carbon emissions along the production chain including scopes 1, 2 and 3. This is Outokumpuneutral by 2050,” says Henrik Lehnhardt.
Through numerous production and quality optimizations as well as the use of biogas, biodiesel, biocoke and low-carbon electricity, we can enormously increase sustainability throughout our entire production.
Hessen Environmental Alliance offers networking and dialogue
The plant in Dillenburg has also been optimized in many places in terms of energy consumption. Smart LEDs react to their environment and thus reduce consumption of electricity, which is generated by wind power. The site also uses a certified environmental and energy management system as well as process waste heat to reduce energy consumption. In addition, the company car fleet is being completely converted to e-mobility in the coming years, and the right to company bicycles has been embedded in the collective employment agreement. The use of wood waste or hydrogen is in planning, and a large solar plant is soon to be built on an adjacent open space.
But as innovative as these ideas are, their implementation and integration into the complex structures of production are sometimes complicated. “Even for us as a large company, this can pose challenges, because we must not lose sight of the economic aspects. So we are all the more pleased about the support from networking with other companies and stakeholders, which enables us to exchange ideas about such processes. The Hessen Environmental Alliance and the support of the Lahn-Dill Chamber of Industry and Commerce have brought us substantially forward in this,” says Henrik Lehnhardt.
In mid-2022, the Hessen Minister for the Environment, Priska Hinz, personally presented the certificate of acceptance into the Environmental Alliance. “We are making Hessen carbon neutral. To do this, we need companies like Outokumpu that participate and invest in climate protection and thus in the future,” says Hinz. The Environmental Alliance was formed over 20 years ago and is an important platform for business, policymakers, and administration to achieve common environmental goals in Hessen. The members work to improve the environmental performance of their companies beyond the legal standards. It currently has 917 Hessen companies as members. In addition to the voluntary commitment, it offers dialogue forums and workshops, for example, on avoiding microplastics from tire and road abrasion or the recycling of building materials, providing excellent opportunities for networking and improvement of environmental and climate protection.
Circular economy as the ultimate goal
For Outokumpu, these goals are a matter of course – and the Finnish company also incorporates them into its products at every level. “Stainless steel has the great advantage that, by melting it down, it can be reused again and again without any loss of quality. In the manufacture of our products, we harness this potential of the circular economy in a targeted manner and achieve a world-leading recycling rate of over 90 percent. Because we achieve the greatest effect in terms of sustainability by simply using fewer products,” says Vice President HR Henrik Lehnhardt.
About Outokumpu
Outokumpu Nirosta GmbH is the German subsidiary of the Finnish company Outokumpu Oyj, which has become one of the world’s largest producers of stainless steel since it took over the stainless steel production from ThyssenKrupp. With around 10,000 employees in 30 countries, including almost 2,000 in Germany and 600 at the Dillenburg site, Outokumpu is the world’s leading supplier of sustainable stainless steel. Its principal place of business is in Helsinki, where the company was founded in 1910.
The Dillenburg site in Central Hessen specializes in the final processing and finishing of flat products made of stainless steel. In the first quarter of 2022, almost 43,000 tons of material were produced here ready for dispatch.